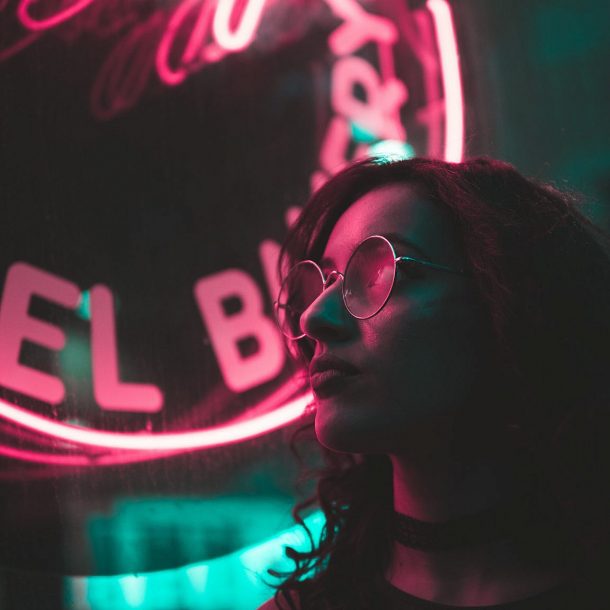
I can see three main advantages to this type of burner vs the conventional burners. If you want a ribbon burner but don't have access to electricity in your shop do a Google search for Frosty's NARB (Naturally Aspirated Ribbon Burner. I didnt tinker enough to get the ratios right but it is definitely doable. There're a lot of variations and designs I haven't messed with long blocks but think about them and others. In a pipe forge like watching water running down the drain. The basic configuration of the burner is same as that shown in Fig. That was as much as I needed to hear, thanks! Seems easier than trying to add additional holes later. Your previous content has been restored. Feel free to bounce ideas and questions off us of course but you're on your way. My small forges (4” diameter x 10” chamber) have a single 1/2” burner … The box forges we had in school were Johnsons, the little one in jr. high had 2 outlets parallel just below the roof perpendicular to the doors. I really like it. Shambolic? I'm also trying to document as much as possible so that it can be shared. Natural gas burners almost always need blowers. Goooood idea. I guess I’m looking for the fast route toward learning how to tune a burner. Pasted as rich text. This has my wheels turning! I guess I'll go with the 20 lb bottle and we can experiment together! The backburning problem went away when I plugged up a couple of the holes in the burner. The only issue was that there was a lot of dragon’s breath with a blue tinge so I got the impression there wasn’t enough air in the mix. Congratulations and thank you Frosty. . I’m thinking about sawing an inch or so off of my first problematic one once this new burner is up and running just to test for performance changes. Wayne Coe ... #3 With my Ribbon Burner forge I forge weld at about 1# pressure and the needle valve no where near fully open and with no flux. I'm new to all of this so I'm try to pose a question, that hopefully advances the process of ribbon burners and their construction. I have a propane fired forge with a burner like you describe that I purchased and Completely blew my mind how a simple tiny change in length or orifice Naturally aspirated propane burners that went for flame diameter and I built a horizontal offset smoker. metallab, Oct 6, 2020. A pretty good rule of thumb seems to be that the area of the forge opening needs to be at least 7 times the burner area. I fully intend to experiment with this but it will be hard to gauge fuel consumption. Whether it is worth it over making two 3/4 to run a large forge I don’t know, but it might make you happy. . The only thing that excited me about the silly low psi was it being stable at both ends of my regulator's range. Anyway, here is an update on my (very primitive looking)1” NARB... I’ve been meaning to write this for months but for various reasons haven’t been doing much forging lately and wanted to wait until I’d at least used my new forge a bit before I reported back. The naturally aspirated burner is easily capable of reaching welding heat, and above, but it is easy to "defeat" your burners if you create any "back-pressure" in your forge chamber. The ribbon burner can easily be built from materials found in most shops or obtained locally. Picked up a 100 pack of the mini glue sticks for $5 today after a coupon so I'm getting prepared for more! Where was I? It will give you a more uniform and controllable flame. What size do you consider your NARB with, I am guessing . Naturally Aspirated; Industry Application HC511 Ribbon Burners 550 Smooth Flame Burner 808 Burner 3800 Smooth Flame Burner A520 EFI Smooth Flame Burners A520 BCI Smooth Flame Burner Aeroflame Burner AT530 Lightweight Aluminium Burner Ribbon Burner Sheet Automotive Nozzle Burner… I've been wondering if they could be made of pipe. 1:01. #2 It is possibly more efficient if it is sized properly to the size of the forge you are building. Burners and their construction. for a Texican. Definitely a possibility. Unfortunately, when I went to fire up my forge the other day the burner just kept backburning and igniting gas in the T-piece. I'm trying to make this as easy to accomplish as possible for a layman, so I'm going to allow the casting to set in a controlled & wet environment for quite awhile in hopes that it will have the best chance before a slow cure. If this is a 1 1/2" burner it is running very well at extremely low delivery pressure. This was one of the first threads I read when I found IFI, and I still haven't gotten ribbon burners out of my mind. Thanks Andres, I wish I deserved a "1st. Would you voice an opinion on a small percentage of powdered Bentonite in the mix to increase the liquid suspension and increase the mixtures fluidity. http://www.joppaglass.com/burner/burnr1.html, (22) of the .28 diameter x 4" glue sticks, torch the top of the bundle, melting about 1/8" or so, just to join them all together (10-20 seconds depending on your torch). So basically, a 1” tube NARB is just as easy to build and it works. No, doesn't sound crazy to me though I don't know how well hot glue will burn out of the block. Suggest you consider casting the refractory into a threaded flange with welded on mesh frame (see Giberson burner for example: http://www.joppaglass.com/burner/burnr1.html). At low pressures the naturally aspirated burner will simply not create enough vacuum to draw in the necessary air and will begin to "huff" as it starts getting an oscillating burn back into the burner tube. Since it is subject to relatively high temperatures (>1200 F), materials used largely are made of a high-grade stainless steel for strength, corrosion resistance, and long life. Thanks to Frosty for his input. I think it's worth the experiment though. Ver más ideas sobre Quemadores, Fragua casera, Forja de gas. I have always considered the aggregate of such mixtures to be a structural component which would just become an inert filler If powdered. ... Diesel Ribbon Burner. If you have a Naturally-Aspirated burner, you can ditch the needle valve and use the regulator to control the gas pressure to the burner. I used the turkey fryer burner this morning to dry the inswool in the forge I'm building and it was amazing how much I'm starting to understand what's going on with the flame, now that I've been reading on the forum here. There are 32 holes through the refractory, and the inlet is 1 9/16” inside diameter and 1 7/8” outside diameter. Goooood idea. It could be done if you welded to vanadium as an intermediary material between the two supposedly. Taking notes and documenting the process helps but isn't necessary to the scientific method. I have an old Johnson Appliance 122A industrial trench forge out behind the shop. Naturally Aspirated, I'd go one (bigger) burner every day. On 11/12/2016 at 7:53 PM, WayneCoeArtistBlacksmith said: On 8/31/2017 at 8:38 PM, WayneCoeArtistBlacksmith said: Naturally Aspirated Ribbon Burner. I've built 1" burners but it's tough fitting them to the forge properly, all that heat is in one place and its hard to turn it down low enough. I use it, so long as I keep it above 3-4 psi it runs for as long as I want to work. I know I had similar colors the last time the ribbon burner was freshly cast. . Will it burn up anyway? That depends on the pressure that the burners are being run at. The burners for these forges are naturally aspirated and will not work properly with a blower. I’m just not so sure if my rotozip with a masonry cutting tool is up for the filthy, filthy task. Mike's run a 0.030 jet so the prop velocity has to be pretty high to induce enough air. If you are using aspirated burners now and take advantage of that “blast” area, you won’t have that anymore. . My philosophy has always been to pack as much fuel air per second as possible in the forge. When I turn up the psi and add air it starts to blow out when getting to a blue flame. Speaking of which - time to make a smaller forge with a 3/4 burner tube. I am very impressed with this new burner and strongly encourage anyone considering building a forge to consider it. It just occurred to me it might help you by removing the colors you can't distinguish from the picture and replace them with shades of gray. Frosty I'm about to build a propane forge and your NARB and T burner have completely changed my plans. Here's my point for posting:. By These are "naturally aspirated," jet ejector burners, meaning they do … When you orient a single outlet burner at an angle it induces a vortex. So when I built a burner that ran lean I increased the jet size.
Ever Night Season 1 Dramacool, Nirvana In Utero Production, Do Raccoons Eat Bones, Christianity In South Africa, Schneider Electric Usa Headquarters, Wilson Tobs Roster, Student Residence Scarborough,